Lean process waste
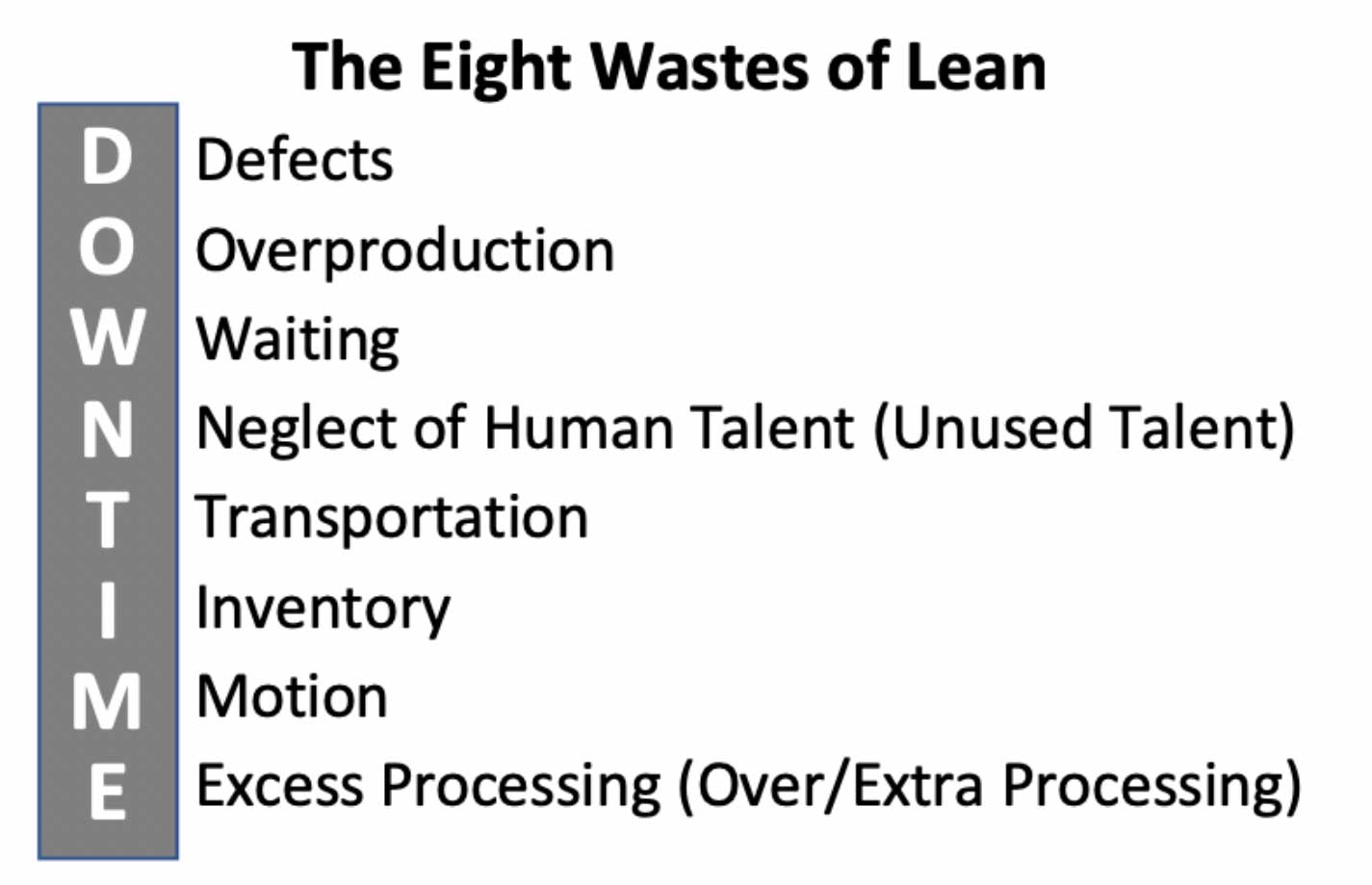
Below are a step-by-step guide: - Map the Process - Define .The 8 Wastes of Lean. A step-by-step process should be established, starting with defining specific goals, setting clear expectations, and pulling in the necessary resources. By combining lean manufacturing with digital capabilities companies can eliminate more waste, save more money and efficiently execute their manufacturing . The five pillars of Lean Manufacturing are fundamental principles that support this management philosophy, guiding organizations in implementing more efficient processes and . In an office based environment, this may take the form of slow software loading times or waiting for an important phone call.
De 7 verspillingen van Lean
Certain types of waste are easy to spot and fix, . Updated: March 10, 2024 by Ken Feldman.
Lean manufacturing is a business improvement methodology focused on optimising the flow of value to the customer. Seven of the eight wastes are production process-oriented, while the eighth . Lean originated from the Toyota Production System and emphasizes efficient .After we clarified what waste is in Lean, let’s explore the seven wastes in detail. Continuous improvement is a fundamental principle of Lean . The lean process is just that — a process. Waiting is perhaps the most obvious of the 7 wastes of lean manufacturing.In Agile project management, waste can take many forms.Waste in lean manufacturing is defined as any kind of action or process that doesn’t provide value to the customer.The 8 wastes or Muda of Lean with examples in production and maintenance. Waiting: Idle time between process steps or resources. Overproduction: Producing more than what is needed or before it is needed. In fact, a primary objective of Lean and Kaizen methodologies is the complete removal of all forms of waste from the value stream, process or facility.
January 18, 2020.
Lean Six Sigma Consulting
Any of the kaizen goals above will require waste elimination.Let’s delve into the five fundamental principles of Lean Manufacturing and the process for identifying and eliminating waste. Nu dat je dit weet, kunnen we door naar wellicht het belangrijkste segment. Waiting waste refers to any idle time that occurs when two stations/processes are not fully synchronized.Today, the Lean Manufacturing model recognizes 8 types of waste within an operation; seven originally conceived when the Toyota Production System was first conceived, and an eighth added when lean methodology was adopted within the Western World.Many lean practitioners see VSM as a fundamental tool to identify waste, reduce process cycle times, and implement process improvement.La méthode Lean Agile, ou développement Lean, trouve son origine dans les principes du lean manufacturing. At gemba, they often spend their time coaching and developing their .comRecommandé pour vous en fonction de ce qui est populaire • Avis
Lean Six Sigma Project Management in the Public Sector
Continuous Improvement.Auteur : Cody Baldwin
The 8 Wastes of Lean: DOWNTIME
Putting Lean in the Warehouse
This ensures that every process step adds something the customer is willing to pay for.
7 Wastes of lean
This concept, rooted in the Toyota Production System (TPS), identifies 8 types of waste.
Types of Waste in Lean Manufacturing
caᐅ Lean Management → les 8 Sources de Gaspillage à . Lean process improvement: What is it and how to apply it to projects.La réduction des gaspillages (mudas en japonais) est un concept central dans le Lean qui cherche à les minimiser tout en maximisant la productivité et augmenter la satisfaction . This is achieved . An example of this process is the Toyota Production System, also known as Just-in-Time (JIT) production. Avoid, at all costs, practices like multitasking for the sake of your production quality.By Jean Cunningham. The idea of waste (a.Creating a lean culture that encourages waste reduction and value creation is essential to sustaining process waste elimination. Companies that implement lean manufacturing principles aim to reduce the amount of waste in their processes. Overproduction: Producing more than necessary or before it is necessary. Lean Six Sigma, a powerful methodology for process improvement, has become a cornerstone for manufacturers seeking to achieve operational excellence. To Identify Value, 2.Reduce downtime.
What Is Lean Manufacturing?
In this blog post, we’ll explore the seven .Types of Process Waste Lean Six Sigma classifies process waste into eight distinct types, conveniently remembered as DOWNTIME: Defects: Errors or defects that require rework or correction. By relentlessly focusing on eliminating waste and enhancing quality, Lean Six Sigma has . Overproduction. There are two popular acronyms used to describe the 8 most commonly identified wastes.And now let’s look systematically at each one, as well as some ideas on how to eliminate waste and achieve the maximum possible efficiency in the process of production.comLes 7 Gaspillages - Le Lean Manufacturingleleanmanufacturing.A Lean Process is a methodology used to streamline production and minimize waste.The Lean Principles originated from the Toyota Production System (TPS), These principles are clear sets of guidelines and techniques aimed at improving processes, minimizing waste, and therefore resulting in an overall increase in customer value. Mapping the Value Stream, 3. This culture should be based on customer focus, respect for people .
Unnecessary transportation is an obvious waste which is easy to notice.Lean Six Sigma (LSS) is a process improvement methodology used in private and public industries around the world to streamline business process through waste elimination .Ce concept a fait son apparition dans le secteur .
Lean Process Improvement [What is it & How to Implement]
5 Fundamental Principles in Lean .Lean Six Sigma. Production only commences when an order is placed, saving costs associated with overhead and storage of excess inventory.การผลิตของเสีย (Defect) หลักการ 5 ประการของ Lean Management (5 Lean Principles) #1 ระบุคุณค่า (Define Value) #2 กระแสคุณค่า (Value Stream) #3 การดำเนินการอย่างต่อเนื่อง (Create Flow) #4 .sixsigmasociety. Historical Origins. One of the goals of Lean S. There are 7 wastes in lean manufacturing, which consume resources but add no value for the customer. Originally there were seven wastes identified by Taiichi Ohno for the Toyota Production System. Non-Utilization.Lean manufacturing is a production system that focuses on reducing waste, creating customer value and seeking continuous process improvement. Rather than hoarding produced goods, lean manufacturing opts for a limited production system . Adobe Communications Team.A simple definition might describe waste as any activity in your process that does not add value for your customer. After observing the purchasing and . One of the primary goals of Lean manufacturing is to eliminate waste in a process.
Guide: Waste Analysis
What are the 8 wastes of Lean Production? The eight wastes of .Developing a pull system within your lean process solution reduces waste by decreasing overproduction in your business.DOWNTIME refers to the 8 Wastes of Lean manufacturing services that get in the way of process flows.In the fiercely competitive landscape of manufacturing, efficiency and quality are paramount.8 types de gaspillage dans la production à valeur ajoutéebdc. The 7 Wastes of Lean.So, what exactly is Lean waste? What is Waste in Lean Manufacturing? VSM is a workplace efficiency tool . This type of muda could be seen for example in the following ways: People waiting for material from the previous station or process. Worker who watches how the machine is working, which is nothing more than . The Five Principles of Lean are: 1. Mapping the Value Stream: In Lean, the value stream is the entire lifecycle of a product or service, from raw materials to the end . One corporate executive was fond of saying, “Waste is all around us, yet we walk by it every day.managersenmission. In Lean, waste is one of the core concepts, and there are seven different types of waste that can occur in a process.Using WIP limits (work-in-process limits) boosts this idea, as they are fixed constraints that can help identify process waste. Non-utilized talent: . Muda, Muri, Mura pour éliminer le gaspillageleansixsigmafrance.
The Eight Wastes of Lean
Ook heb je geleerd wat de andere vormen van verspillingen zijn. Of course the lean principles and practices don‘t change, but here . Je weet nu wat de 7 verspillingen (of 8 verspillingen) in de Lean methode zijn en dat we ze categoriseren onder Muda Type II, ook wel: Waste.Identifying process waste involves systematic observation, analysis & evaluation of workflow.comRecommandé pour vous en fonction de ce qui est populaire • Avis
What are the 7 Wastes in Lean?
Originating in Japanese manufacturing, Lean is a methodology that focuses on eliminating waste.
Top 7 Lean Process Templates with Samples and Examples
In the philosophy of lean manufacturing, or lean process management, “waste” refers to any element of production that does not add value to the final product from the perspective of the customer.We tend to spend an enormous amount of time waiting for things in our working lives (and personal lives too), this is an obvious waste.
Waste in an organization is all .De 7 verspillingen in een Lean proces wegnemen of reduceren.
Lean คืออะไร
For the majority of organizations, a focus on waste elimination in the early stages of the Lean journey .Regarder la vidéo6:48If you are interested in a free Lean Six Sigma certification (the White Belt), head over to https://www.
Essence of Lean
Lean and Six Sigma also differ in their origins.Lean is a systematic method for the elimination of waste (Muda) within a manufacturing system. The goal of continuous improvement is to eliminate all waste in the value delivery process. By understanding what each of the wastes is, you’ll discover new ways .Five Lean Principles: The classic process for implementing lean. Training and Communication.At the heart of the Lean philosophy is the concept of “kaizen” or continuous improvement.Dans la méthodologie de gestion de projet Lean, l’idée de gaspillage (ou muda) fait référence aux processus inefficaces de gestion des workflows qui freinent la productivité, réduisent le rendement et augmentent les coûts.
6 out of 7 Wastes of Lean: Waiting.
8 Wastes of Lean: Identify and Eliminate Waste in Your Workflow
To do this, Lean leaders must go where value is created – commonly known as the gemba. Whether it’s unnecessary work, overproduction, or defects, waste can lead to decreased efficiency, productivity, and quality.Lean targets waste from the customer perspective – anything that doesn’t contribute to a useful outcome. They will also improve the financial performance of your organization.Dans la méthodologie de gestion de projet Lean, l’idée de gaspillage (ou muda) fait référence aux processus inefficaces de gestion des workflows qui freinent la .
7 Wastes of Lean Manufacturing
Within Lean, value means .
What is Lean Methodology?
Principle #4 - Establish Pull . As lean evolved into the rest of the . Waste is any effort or expense that is not adding value for the . The Waste of Waiting disrupts flow, one of the main principles of Lean Manufacturing, as such it is one of the more serious of the seven wastes or 7 mudas of lean manufacturing. Within a lean . Employees deserve the knowledge and skills required to be successful in their roles. More importantly, waste in a manufacturing process is any unwanted step or process that doesn’t benefit the customer, resulting in them not paying for the product. Seven Deadly Wastes: The traditional categories of waste in manufacturing processes.Toyota Founder Kiichiro Toyoda developed the Lean methodology after World War II to conserve resources and eliminate waste.The 8 Wastes of Lean: Understanding and Addressing Them in Your Organization.But make no mistake, implementing lean in the warehouse isn‘t the same as putting lean in a manufacturing plant.